Journal Description
Machines
Machines
is an international, peer-reviewed, open access journal on machinery and engineering published monthly online by MDPI. The IFToMM is affiliated with Machines and its members receive a discount on the article processing charges.
- Open Access— free for readers, with article processing charges (APC) paid by authors or their institutions.
- High Visibility: indexed within Scopus, SCIE (Web of Science), Inspec, and other databases.
- Journal Rank: JCR - Q2 (Engineering, Mechanical) / CiteScore - Q2 (Control and Optimization)
- Rapid Publication: manuscripts are peer-reviewed and a first decision is provided to authors approximately 15.5 days after submission; acceptance to publication is undertaken in 2.6 days (median values for papers published in this journal in the second half of 2024).
- Recognition of Reviewers: reviewers who provide timely, thorough peer-review reports receive vouchers entitling them to a discount on the APC of their next publication in any MDPI journal, in appreciation of the work done.
Impact Factor:
2.1 (2023);
5-Year Impact Factor:
2.2 (2023)
Latest Articles
The Spatio-Temporal Equalization Sliding-Window Distribution Distance Maximization Based on Unsupervised Learning for Online Event-Related Potential-Based Brain–Computer Interfaces
Machines 2025, 13(4), 282; https://doi.org/10.3390/machines13040282 (registering DOI) - 29 Mar 2025
Abstract
Brain–computer interfaces (BCIs) provide a direct communication pathway between the central nervous system and external environments, enabling human–machine interaction control. Among them, event-related potential (ERP)-based BCIs are among the most accurate and reliable BCI systems. However, current mainstream classification algorithms struggle to eliminate
[...] Read more.
Brain–computer interfaces (BCIs) provide a direct communication pathway between the central nervous system and external environments, enabling human–machine interaction control. Among them, event-related potential (ERP)-based BCIs are among the most accurate and reliable BCI systems. However, current mainstream classification algorithms struggle to eliminate calibration requirements and rely heavily on costly labeled data, limiting the practical usability of ERP-based BCIs. To address this, the development of unsupervised algorithms is critical for advancing real-world BCI applications. In this study, we propose the spatio-temporal equalization sliding-window distribution distance maximization (STE-sDDM) algorithm, which introduces spatio-temporal equalization (STE) to unsupervised ERP classification for the first time and integrates it with a novel unsupervised classification method, sliding-window distribution distance maximization (sDDM). STE estimates and removes colored noise interference in background noise to enhance the signal-to-noise ratio of inputs for sDDM. Meanwhile, sDDM leverages an enhanced inter-class divergence metric based on the ergodic hypothesis theory, utilizing sliding windows to emphasize temporally discriminative features, thereby improving unsupervised classification accuracy. The experimental results demonstrate that the integration of STE and sDDM significantly enhances ERP feature separability, outperforming state-of-the-art unsupervised online classification algorithms in spelling accuracy and the information transfer rate (ITR), facilitating more accurate and faster plug-and-play real-time control for BCI systems. Additionally, static spatio-temporal equalizer architectures were found to outperform dynamic architectures when combined with this framework.
Full article
(This article belongs to the Topic Theoretical and Applied Problems in Human-Computer Intelligent Systems)
►
Show Figures
Open AccessArticle
Modeling and Analysis of Gyroscope Air-Floating Support Assembly Precision Under Uncertain Process Loads
by
Yang Yang, Bo Yuan, Xiaokai Mu, Yingjie Zhao and Qingchao Sun
Machines 2025, 13(4), 281; https://doi.org/10.3390/machines13040281 (registering DOI) - 28 Mar 2025
Abstract
Air-floating supports are the core component of precision gyroscopes. The precision of their assembly directly determines the degree of gyroscope drift and plays a decisive role in the device’s output precision and service life. Existing air-floating support assembly precision analysis techniques have not
[...] Read more.
Air-floating supports are the core component of precision gyroscopes. The precision of their assembly directly determines the degree of gyroscope drift and plays a decisive role in the device’s output precision and service life. Existing air-floating support assembly precision analysis techniques have not yet considered interface deformation, resulting in poor theoretical accuracy and large deviations in actual performance. To address the issue of imprecise predictions in assembly precision for air-floating supports under process loads, this study performs a predictive analysis and impact assessment of assembly precision with uncertainties in the connection process. Firstly, based on bolt elastic interactions, a method for calculating interface assembly deformations is proposed and integrated into a predictive model under process loads. Secondly, numerical computations and assembly deformation tests are carried out to confirm the model’s accuracy. Finally, the distribution law of gyroscope drift is analyzed, considering uncertainty in the connection process. The results show that the maximum deviation of the assembly accuracy prediction model for air-floating supports is less than 5%. Drift in air-floating supports under normally distributed loads shows a skewed normal distribution pattern; the mean drift value decreased sequentially from about 0.03023°/h/g to 0.01995°/h/g, which was reduced by 34% with variation in the dispersion of the pretension force (from 15% to 5%). These findings provide novel insights to enhance assembly precision processes and optimize the fabrication of high-end, complex equipment.
Full article
(This article belongs to the Section Machines Testing and Maintenance)
Open AccessReview
Recent Advances in Lean Techniques for Discrete Manufacturing Companies: A Comprehensive Review
by
Xinyan Yang, Lei Fu, Ling Zhu and Jiufang Lv
Machines 2025, 13(4), 280; https://doi.org/10.3390/machines13040280 - 28 Mar 2025
Abstract
Background: Against the backdrop of the transformation and upgrading of the manufacturing industry, lean manufacturing has emerged as a systematic and advanced production paradigm that has deeply permeated the entire value chain of enterprises. Objective: However, there is a lack of systematic and
[...] Read more.
Background: Against the backdrop of the transformation and upgrading of the manufacturing industry, lean manufacturing has emerged as a systematic and advanced production paradigm that has deeply permeated the entire value chain of enterprises. Objective: However, there is a lack of systematic and effective lean technology paradigms in aspects such as lean practice processes and improving manufacturing process efficiency. Moreover, a comprehensive analysis of the current status and development strategies of lean technologies in discrete manufacturing enterprises has yet to be conducted to address issues such as the fragmentation of lean technology applications and the ambiguity of implementation strategies in discrete manufacturing enterprises. Methods: This paper conducts an extensive review of the literature on lean technologies and transformation methods in discrete manufacturing enterprises. A multi-stage data analysis approach (including data identification, screening, eligibility assessment, classification, and comprehensive analysis) is utilized to analyze 369 highly relevant documents. Results: The main contributions of this study are as follows: (1) A comprehensive review of existing lean manufacturing technologies and methods is provided, classifying, comparing, and summarizing the current status of lean technology and strategy applications, and delineating nine categories of lean technology application directions. (2) A “5P” theoretical framework (Philosophy, Process, People, Problem-solving, and Product) is proposed, redefining a lean technology framework that covers the value streams of discrete manufacturing. (3) Future application trends of lean technologies in discrete manufacturing are summarized and predicted, and an implementation strategy for lean technologies tailored to small and medium-sized discrete manufacturing enterprises, along with six lean technology development strategies, are proposed. The results indicate that many enterprises have derived diversified methods based on their own circumstances, which compensate for the deficiencies of the original lean models. Discussion and Conclusions: This paper organizes these methods to serve as a reference for future research on the lean technology system. The proposed strategies include formulating lean transformation strategies for discrete manufacturing enterprises, enhancing proactive lean capabilities, adapting to passive lean factors, and creating value for the enterprises’ reasonable lean needs from three levels: strategic philosophy, objective principles, and tool technologies. This research will play a guiding role in promoting the coordinated development of lean implementation and achieving high-quality development in discrete manufacturing enterprises.
Full article
(This article belongs to the Section Advanced Manufacturing)
Open AccessArticle
Maintenance of Arc Occurrence at the End of the Stator Slot in a High-Voltage Motor
by
Hoyeol Yoon and Youngchul Bae
Machines 2025, 13(4), 279; https://doi.org/10.3390/machines13040279 - 28 Mar 2025
Abstract
This study investigates the critical issue of arc-induced partial discharge in high-voltage motor stator windings and proposes a cost-effective, targeted maintenance approach to mitigate these effects. Diagnostic techniques, including insulation resistance tests, tan δ measurements, partial discharge analyses, and UV camera inspections, were
[...] Read more.
This study investigates the critical issue of arc-induced partial discharge in high-voltage motor stator windings and proposes a cost-effective, targeted maintenance approach to mitigate these effects. Diagnostic techniques, including insulation resistance tests, tan δ measurements, partial discharge analyses, and UV camera inspections, were employed to identify and assess fault points. A novel partial maintenance method involving felt-pad insulation reinforcement was implemented to address the arc discharge issues. Post-maintenance diagnostics confirmed a significant reduction in partial discharge levels, with an average decrease of over 80%, demonstrating the effectiveness of the proposed approach. Compared to traditional rewinding methods, this technique offers substantial savings in time and cost while enhancing motor reliability. The findings underscore the importance of precise diagnostics and tailored interventions in extending the lifespan and operational stability of high-voltage motors, providing practical insights for industrial maintenance strategies.
Full article
(This article belongs to the Special Issue New Trends in Reliability and Lifetime Improvement in Power-Electronic-Controlled Machines and Devices)
Open AccessArticle
Rolling Bearing Fault Diagnosis Based on Wavelet Overlapping Group Shrinkage and Extended Envelope Hierarchical Multiscale-Weighted Permutation Entropy
by
Runfang Hao, Yunpeng Bai, Kun Yang, Zhongyun Yuan, Shengjun Chang, Mingyu Wang, Hairui Feng and Yongqiang Cheng
Machines 2025, 13(4), 278; https://doi.org/10.3390/machines13040278 - 28 Mar 2025
Abstract
Rolling bearing vibration signals contain rich fault feature information. However, their periodic pulse feature is often interfered with by strong background noise, which reduces the feature recognition ability of fault diagnosis strategies. Therefore, accurately extracting periodic pulse information under strong background noise is
[...] Read more.
Rolling bearing vibration signals contain rich fault feature information. However, their periodic pulse feature is often interfered with by strong background noise, which reduces the feature recognition ability of fault diagnosis strategies. Therefore, accurately extracting periodic pulse information under strong background noise is a key challenge in rolling bearing fault diagnosis. To address this, a fault feature extraction strategy combining wavelet overlapping group shrinkage (WOGS) and extended enveloped hierarchical multiscale-weighted permutation entropy (EEHMWPE) is proposed. First, wavelet decomposition is applied to decompose original vibration signals into wavelet coefficients, with WOGS adaptively adjusting the shrinkage level based on energy relationships to effectively suppress noise. Next, for the denoised signal, EEHMWPE extracts periodic pulse features by integrating envelope analysis, weighting, and extended statistical features. Envelope processing enhances fault-induced impulses, the weighting scheme highlights dominant fault patterns, and extended statistical features further improve the class separability between normal and fault signals. Finally, the strategy was validated on the bearing test bench, CWRU, and HUST datasets, all of which achieved over 99% accuracy with superior feature recognition.
Full article
(This article belongs to the Section Machines Testing and Maintenance)
►▼
Show Figures
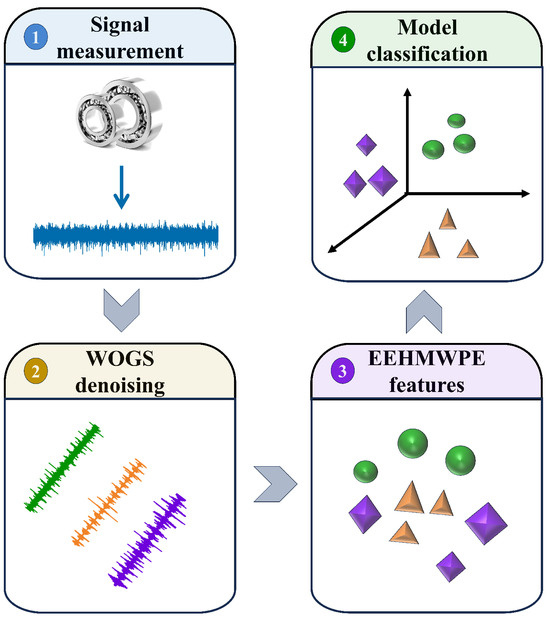
Figure 1
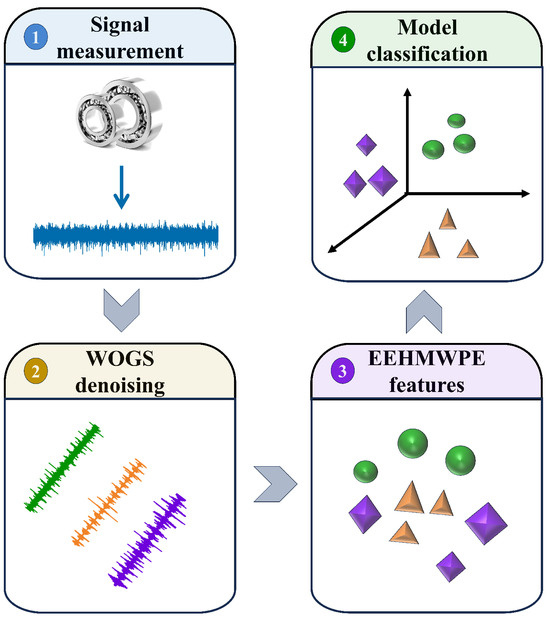
Figure 1
Open AccessArticle
A Strain-Based Method to Estimate Rolling Tire Grounding Parameters and Vertical Force
by
Jintao Zhang, Zhecheng Jing, Haichao Zhou, Haoran Li and Guolin Wang
Machines 2025, 13(4), 277; https://doi.org/10.3390/machines13040277 - 28 Mar 2025
Abstract
The tire grounding parameters are a crucial component of the vehicle dynamics control system; accurate acquisition of grounding parameters is important for improving traction, braking force, and handling stability during vehicle operation. This paper studies strain-based intelligent tire contact patch length and vertical
[...] Read more.
The tire grounding parameters are a crucial component of the vehicle dynamics control system; accurate acquisition of grounding parameters is important for improving traction, braking force, and handling stability during vehicle operation. This paper studies strain-based intelligent tire contact patch length and vertical force estimation; first, a 205/55R16 radial tire was established, and static grounding experiments were carried out to verify the validity of the finite element model. Second, the sensitivity of the circumferential strain signal of the inner liner in the contact area of a tire with complex tread patterns was discussed. Methods for estimating the contact angle and contact patch length of rolling tires were established, and the estimation accuracy under different tire parameters and operating conditions were analyzed. Finally, the vertical force-sensitive response characteristics were analyzed and extracted, and the vertical force prediction model of a radial tire based on particle swarm optimization BP neural network was established.
Full article
(This article belongs to the Section Vehicle Engineering)
►▼
Show Figures
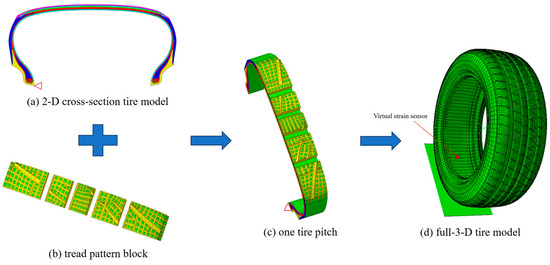
Figure 1
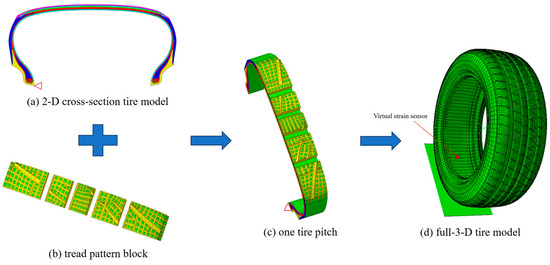
Figure 1
Open AccessArticle
Tool Condition Monitoring in the Milling of Low- to High-Yield-Strength Materials
by
Sohan Nagaraj and Nancy Diaz-Elsayed
Machines 2025, 13(4), 276; https://doi.org/10.3390/machines13040276 - 27 Mar 2025
Abstract
The preservation and continuous monitoring of cutting tools in a computer numerical control (CNC) machine is essential for ensuring seamless transitions in the manufacturing workflow, as well as maintaining adequate part quality. The implementation of tool condition monitoring (TCM) when milling can provide
[...] Read more.
The preservation and continuous monitoring of cutting tools in a computer numerical control (CNC) machine is essential for ensuring seamless transitions in the manufacturing workflow, as well as maintaining adequate part quality. The implementation of tool condition monitoring (TCM) when milling can provide the user with necessary data regarding tool life, wear, and part quality. However, it is important to broaden the application of the TCM process across a much broader class of workpiece materials to understand the effects of material properties on the condition of the tool. The aim of this paper is to investigate the efficacy of tool condition monitoring techniques while milling low- and high-yield-strength materials across varied process parameters. A Fast Fourier Transform (FFT) analysis was conducted in this research. Vibration data were acquired from both uniaxial and triaxial accelerometers to investigate irregularities in vibrational amplitudes between new and worn milling tools. The experimental results show that there is a significant increase in vibrational amplitudes for the worn tool when compared to the new tool across various frequencies, which affirms the expected increase in vibrations and cutting forces at the tool–workpiece interface from using a worn tool. The F-values and p-values calculated using an F-test with a 95% confidence interval indicated statistically significant differences in vibration data between new and worn tools across various materials, including polyurethane foam, aluminum 6061, mild steel, and stainless steel, under different cutting conditions (low, medium, and high). These results further validate the findings obtained from the FFT analysis and highlight the effectiveness of vibration-based monitoring in distinguishing tool wear under varying material characteristics and machining conditions.
Full article
(This article belongs to the Special Issue Innovations in the Design, Simulation, and Manufacturing of Production Systems)
►▼
Show Figures
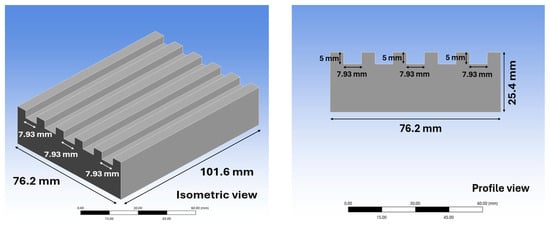
Figure 1
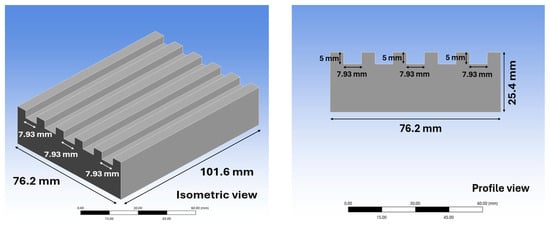
Figure 1
Open AccessArticle
End-to-End Intelligent Adaptive Grasping for Novel Objects Using an Assistive Robotic Manipulator
by
Zhangchi Ding, Amirhossein Jabalameli, Mushtaq Al-Mohammed and Aman Behal
Machines 2025, 13(4), 275; https://doi.org/10.3390/machines13040275 - 26 Mar 2025
Abstract
This paper presents the design and implementation of the motion controller and adaptive interface for the second generation of the UCF-MANUS intelligent assistive robotic manipulator system. Based on extensive user studies of the system, several features were implemented in the interface that could
[...] Read more.
This paper presents the design and implementation of the motion controller and adaptive interface for the second generation of the UCF-MANUS intelligent assistive robotic manipulator system. Based on extensive user studies of the system, several features were implemented in the interface that could reduce the complexity of the human–robot interaction while also compensating for the deficits in different human factors, such as working memory, response inhibition, processing speed, depth perception, spatial awareness, and contrast sensitivity. To effectively and safely control the robotic arm, we designed several new features, including an adaptive human–robot interaction framework. To provide the user with a less complex and safer interaction with the robot, we added new functionalities such as ‘One-click mode’, ‘Move suggestion mode’, and ‘Gripper Control Assistant’. Furthermore, to equip our assistive robotic system with an adaptive User Interface, we designed and implemented compensators such as ‘Contrast Enhancement’, ‘Object Proximity Velocity Reduction’, and ‘Orientation Indicator’. Results from a multitude of experiments show that the system is indeed robust, safe, and computationally efficient in addition to addressing the user’s highly desired capabilities.
Full article
(This article belongs to the Special Issue Advances in Assistive Robotics)
►▼
Show Figures
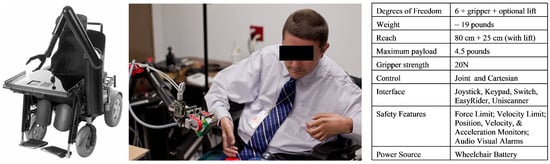
Figure 1
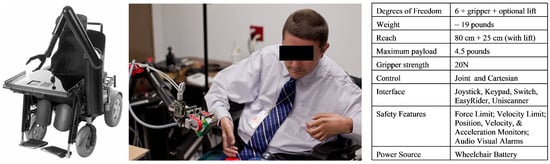
Figure 1
Open AccessArticle
Multi-Indicator Heuristic Evaluation-Based Rapidly Exploring Random Tree Algorithm for Robot Path Planning in Complex Environments
by
Wenqiang Wu, Chuixin Kong, Zhongmin Xiao, Qianping Huang, Mingfeng Yu and Zhiye Ren
Machines 2025, 13(4), 274; https://doi.org/10.3390/machines13040274 - 26 Mar 2025
Abstract
This paper introduces a multi-indicator heuristic evaluation-based rapidly exploring random tree (MIHE-RRT) algorithm to address the key challenges of robot path planning in complex environments. The core innovation lies in a novel dual optimization framework that combines Hammersley sequence sampling with a comprehensive
[...] Read more.
This paper introduces a multi-indicator heuristic evaluation-based rapidly exploring random tree (MIHE-RRT) algorithm to address the key challenges of robot path planning in complex environments. The core innovation lies in a novel dual optimization framework that combines Hammersley sequence sampling with a comprehensive multi-indicator heuristic evaluation mechanism. The Hammersley sequence ensures uniform coverage of the configuration space, while the multi-indicator heuristic evaluation mechanism intelligently guides tree expansion through a three-dimensional evaluation system incorporating diversity, distance, and angle values. After generating the initial path, a pruning algorithm removes redundant points to produce an efficient and practical final path. Extensive experimental validation in four different environmental scenarios (semi-enclosed, maze, chaotic, and crowded) demonstrates that MIHE-RRT outperforms RRT (rapidly exploring random tree), IBi-RRT (improved bidirectional rapidly exploring random tree), and HB-RRT (halton biased rapidly exploring random tree) algorithms. Results show significant improvements in planning efficiency (54–88% reduction in execution time), path quality (15–24% shorter paths), and computational resource utilization (77–94% reduction in nodes). These excellent performance metrics not only prove MIHE-RRT’s advantages in complex environments but also make it particularly suitable for practical robot navigation applications requiring reliable and efficient path planning.
Full article
(This article belongs to the Special Issue Climbing Robots: Scaling Walls with Precision and Efficiency)
►▼
Show Figures
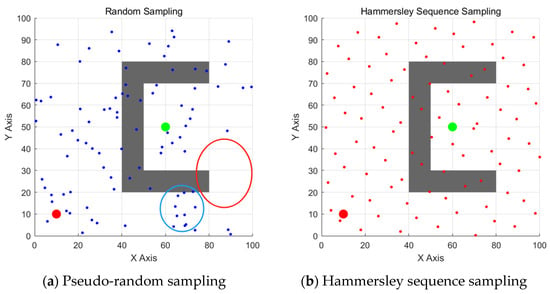
Figure 1
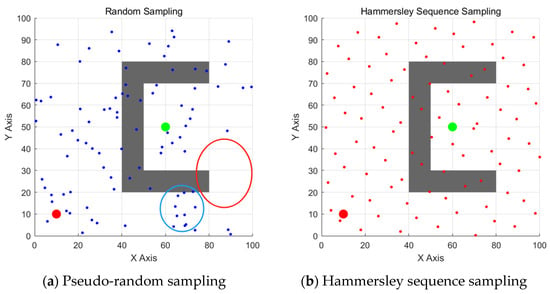
Figure 1
Open AccessArticle
Comparative Study of Dual-Stator Permanent Magnet Machines with Different PM Arrangements and Rotor Topologies for Aviation Electric Propulsion
by
Minchen Zhu, Lijian Wu, Dongliang Liu, Yiming Shen, Rongdeng Li and Hui Wen
Machines 2025, 13(4), 273; https://doi.org/10.3390/machines13040273 - 26 Mar 2025
Abstract
The dual-stator permanent magnet (DSPM) machine has proved to have high space utilization and a redundant structure, which can be beneficial to improving the fault tolerance and torque density performance. In this paper, three types of DSPM machines are proposed and compared, where
[...] Read more.
The dual-stator permanent magnet (DSPM) machine has proved to have high space utilization and a redundant structure, which can be beneficial to improving the fault tolerance and torque density performance. In this paper, three types of DSPM machines are proposed and compared, where two sets of armature windings are wound in both inner/outer stators, producing more than one torque component compared with single-stator PM machines. The machine topology and operating principle of three DSPM machines are analyzed first. Next, feasible stator/rotor-pole number combinations are compared and determined. Furthermore, based on the finite-element (FE) method, both the electromagnetic performances of three DSPM machines under open-circuit and rated-load conditions after optimization are compared, aimed at generating maximum torque at fixed copper loss. The FE analyses indicate that the dual-stator consequent-pole permanent magnet (DSCPPM) machine generates maximum torque per PM volume, together with relatively high efficiency, which makes it a potentially hopeful candidate for low-speed and high-torque applications. In addition, a thermal analysis is carried out to confirm the validity of the design scheme. Finally, in order to verify the FE predictions, a prototype DSCPPM machine is manufactured and experimentally tested.
Full article
(This article belongs to the Special Issue Design, Performance Optimization and Application of Permanent Magnet Motors)
►▼
Show Figures
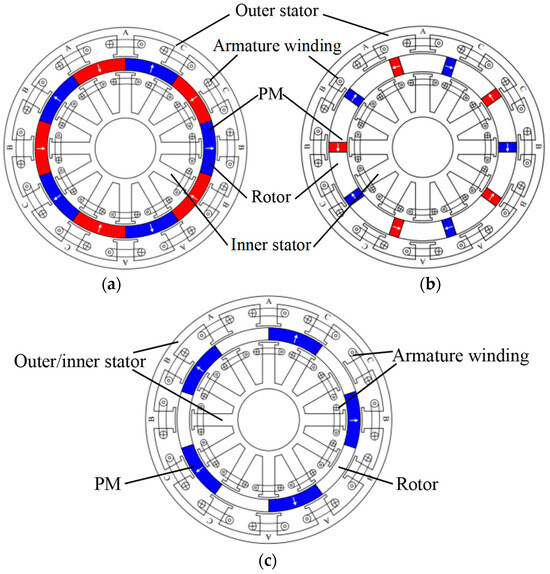
Figure 1
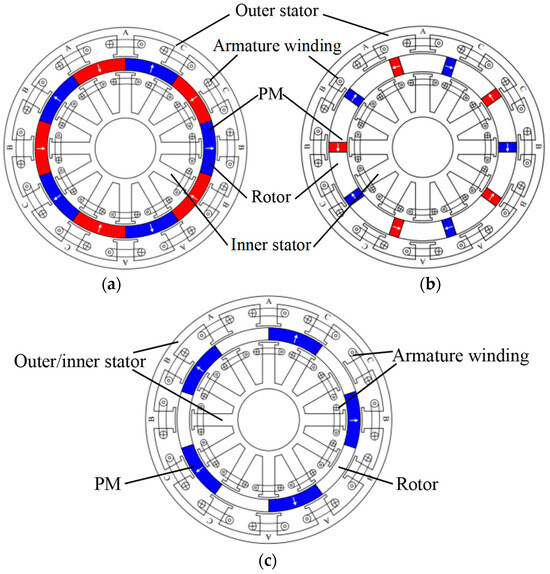
Figure 1
Open AccessArticle
Dynamic Modeling and Numerical Analysis of Gear Transmission System with Localized Defects
by
Yixuan Zeng, Junhui Zhu, Yaoyao Han, Donghua Qiu, Wei Huang and Minmin Xu
Machines 2025, 13(4), 272; https://doi.org/10.3390/machines13040272 - 26 Mar 2025
Abstract
Localized defects are common in gear transmission systems and can sometimes cause serious production problems or even catastrophic accidents. To reveal the failure mechanisms and study the localized defects in gear transmission systems, a 24-degree-of-freedom (DOF) dynamic coupling model is proposed considering shafts,
[...] Read more.
Localized defects are common in gear transmission systems and can sometimes cause serious production problems or even catastrophic accidents. To reveal the failure mechanisms and study the localized defects in gear transmission systems, a 24-degree-of-freedom (DOF) dynamic coupling model is proposed considering shafts, bearings, and gears. The dynamic characteristics of the established model when defects appear on the raceways of bearings and surfaces of gears are analyzed. It can be found in the results that the response of the established model produces periodic shocks when localized defects appear on bearings or gears through numerical analysis. Sidebands generated by fault frequencies can be detected from the frequency spectrum. Especially, bearing-localized defects on the inner race and gear surface are similar in modulation form envelope analysis, and the increase in rotating frequency leads to difficulties in distinguishing defects on bearings and gears. The established coupling dynamic model was validated through experimentation and offers a theoretical basis for the fault diagnosis of gear transmission systems.
Full article
(This article belongs to the Section Machine Design and Theory)
►▼
Show Figures
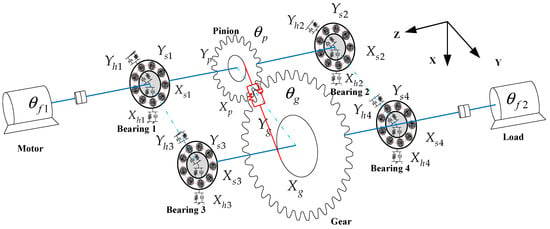
Figure 1
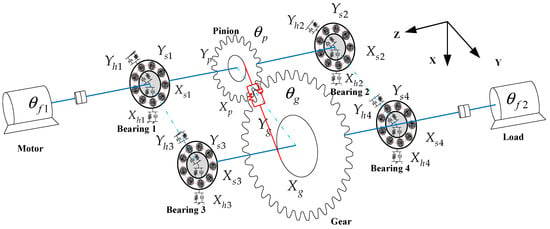
Figure 1
Open AccessArticle
Improving Vehicle Dynamics: A Fractional-Order PIλDμ Control Approach to Active Suspension Systems
by
Zongjun Yin, Chenyang Cui, Ru Wang, Rong Su and Xuegang Ma
Machines 2025, 13(4), 271; https://doi.org/10.3390/machines13040271 - 25 Mar 2025
Abstract
This paper presents a comprehensive vehicle model featuring an active suspension system integrated with semi-active seat and engine mounting controls. The time-domain stochastic excitation of the four tires was modeled using the filtered white noise method, and the required road excitation was simulated
[...] Read more.
This paper presents a comprehensive vehicle model featuring an active suspension system integrated with semi-active seat and engine mounting controls. The time-domain stochastic excitation of the four tires was modeled using the filtered white noise method, and the required road excitation was simulated using MATLAB software R2022b. Four comprehensive performance indices, including engine dynamic displacement, vehicle body acceleration, suspension dynamic deflection, and tire dynamic displacement, were selected and made dimensionless by the performance indices of a passive suspension under the same working conditions to construct the fitness function. A fractional-order PIλDμ (FOPID) controller was proposed, and its structural parameters were optimized using a gray wolf optimization algorithm. Furthermore, the optimized FOPID controller was evaluated under five road conditions, and its performance was compared with integer-order PID control and passive suspensions. The results demonstrate that the FOPID controller effectively improves the smoothness of the vehicle by reducing engine mounting deflection, vehicle body acceleration, suspension deflection, and tire displacement. Moreover, the simulation results indicate that, compared to the passive suspension, the FOPID-controlled suspension achieves an average optimization of over 42% in the root mean square (RMS) of body acceleration under random road conditions, with an average optimization of more than 38% for suspension deflection, 4.3% for engine mounting deflection, and 2.5% for tire displacement. In comparison to the integer-order PID-controlled suspension, the FOPID-controlled suspension demonstrates an average improvement of 28% in the RMS of acceleration and a 2.1% improvement in suspension deflection under random road conditions. However, the engine mounting deflection and tire displacement are reduced by 0.05% and 0.3%, respectively. FOPID control has better performance in vehicle acceleration control but shows asymmetrical effects on tire dynamic deflection.
Full article
(This article belongs to the Special Issue Advances in Vehicle Suspension System Optimization and Control)
►▼
Show Figures
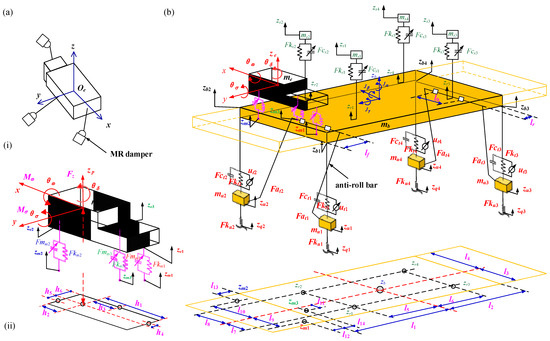
Figure 1
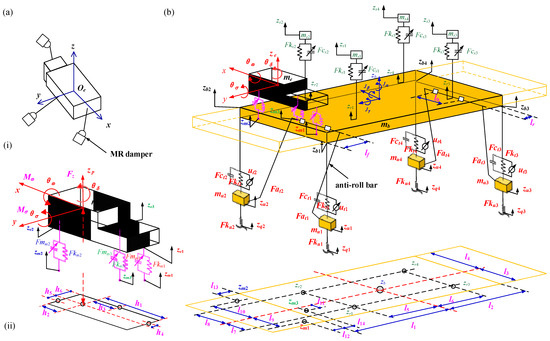
Figure 1
Open AccessArticle
Improved Optimized Minimum Generalized Lp/Lq Deconvolution and Application to Bearing Fault Detection
by
Na Yang, Zhigang Pan and Yuanbo Xu
Machines 2025, 13(4), 270; https://doi.org/10.3390/machines13040270 - 25 Mar 2025
Abstract
Locating the fault-induced cyclic impulses from corrupted vibration signals is a key step in detecting bearing fault characteristics. Recently, a novel deconvolution technique named the optimized minimum generalized Lp/Lq deconvolution (OMGD) was proposed and has been validated as a useful
[...] Read more.
Locating the fault-induced cyclic impulses from corrupted vibration signals is a key step in detecting bearing fault characteristics. Recently, a novel deconvolution technique named the optimized minimum generalized Lp/Lq deconvolution (OMGD) was proposed and has been validated as a useful technique to highlight the periodic impulses related to bearing faults. However, the performance of the OMGD is associated with the appropriate selection of prior parameters, such as the filter length. In addition, the OMGD faces edge effect issues, leading to a shorter duration of the enhanced signal when compared to the measured signal. To overcome the shortcomings of the OMGD, this study proposes an improved version, termed the IOMGD. The enhanced technique employs an advanced sparrow search algorithm to automatically ascertain the filter length, doing away with the need for a predetermined fixed value. To solve the problem of the edge effect, a data extension technique based on the autoregressive model (AR-DET) is proposed to adaptively recover the length of the filtered signal to match that of the raw signal based on the properties observed at the filtered signal. The IOMGD’s superiority over the original OMGD has been substantiated by its performance on various real-world bearing fault datasets. Furthermore, a comparative analysis is performed between the IOMGD and other commonly used bearing fault diagnosis methods, revealing the superiority of the IOMGD.
Full article
(This article belongs to the Section Machines Testing and Maintenance)
►▼
Show Figures
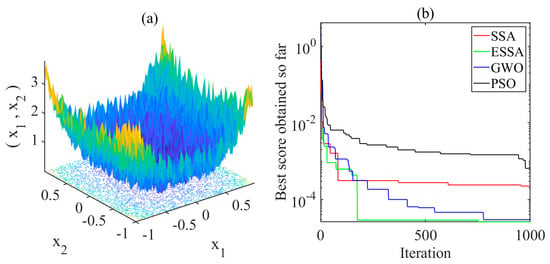
Figure 1
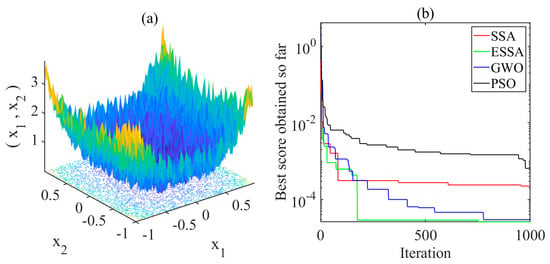
Figure 1
Open AccessArticle
Detecting Particle Contamination in Bearings of Inverter-Fed Induction Motors: A Comparative Evaluation of Monitoring Signals
by
Tomas Garcia-Calva, Óscar Duque-Perez, Rene J. Romero-Troncoso, Daniel Morinigo-Sotelo and Ignacio Martin-Diaz
Machines 2025, 13(4), 269; https://doi.org/10.3390/machines13040269 - 25 Mar 2025
Abstract
In induction motor bearings, distributed faults are prevalent, often resulting from factors such as inadequate lubrication and particle contamination. Unlike localized faults, distributed faults produce complex and unpredictable motor signal behaviors. Although existing research predominantly addresses localized faults in mains-fed motors, particularly single-point
[...] Read more.
In induction motor bearings, distributed faults are prevalent, often resulting from factors such as inadequate lubrication and particle contamination. Unlike localized faults, distributed faults produce complex and unpredictable motor signal behaviors. Although existing research predominantly addresses localized faults in mains-fed motors, particularly single-point defects, a comprehensive investigation into particle contamination in bearings of inverter-fed motors is essential for a more accurate understanding of real-world bearing issues. This paper conducts a comparative analysis of vibration, stator current, speed, and acoustic signals to detect particle contamination through signal analysis across three domains: time, frequency, and time-frequency. These domains are analyzed to assess and compare the characteristics of each monitored signal in the context of bearing wear detection. The data were collected from both steady-state and startup transients of an induction motor controlled by a variable frequency drive. The experimental results highlight the most significant characteristics of each monitored signal, evaluated across the different domains of analysis. The primary conclusion indicates that, in inverter-fed motors, sound and vibration signals exhibit abnormal levels when the bearing is damaged but the related-fault signature becomes complicated. Additionally, the findings demonstrate that the analysis of startup stator current and speed signals presents the potential to detect distributed bearing damage in inverter-fed induction motors.
Full article
(This article belongs to the Special Issue Vibration Detection of Induction and PM Motors)
►▼
Show Figures
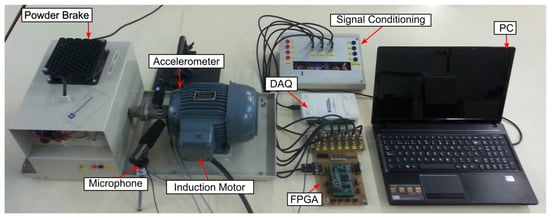
Figure 1
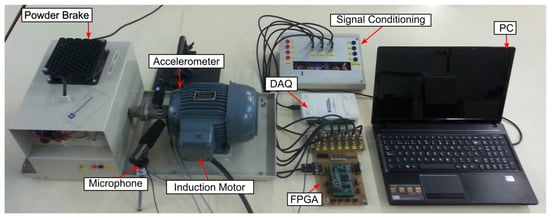
Figure 1
Open AccessArticle
Development and Application of a Dual-Robot Fabrication System in Figuring of a 2.4 m × 4.58 m CFRP Antenna Reflector Surface
by
Qiang Xin, Haitao Liu, Jieli Wu, Liming Lu, Xufeng Hao, Zhige Zeng and Yongjian Wan
Machines 2025, 13(4), 268; https://doi.org/10.3390/machines13040268 - 25 Mar 2025
Abstract
The demand for large-scale components continues to grow with the development of frontier technologies. Traditionally, these components are machined using machine tools, which are costly and have functional limitations. High-flexibility robots provide a cost-effective solution for machining large-scale components. This research proposes a
[...] Read more.
The demand for large-scale components continues to grow with the development of frontier technologies. Traditionally, these components are machined using machine tools, which are costly and have functional limitations. High-flexibility robots provide a cost-effective solution for machining large-scale components. This research proposes a dual-robot fabrication system for producing a 2.4 m × 4.58 m carbon fiber reinforced polymer (CFRP) antenna reflector. First, the kinematic model of the in-house developed robot was established to compute its theoretical workspace, which was subsequently used to partition the machining regions. Based on laser tracker measurements and theoretical calculations, a method and procedure for calibrating the Tool Center Point and Tool Control Frame of the robot were proposed. Subsequently, the dual-robot fabrication system was configured based on the determined machining regions for each robot. To further improve the figuring accuracy of the system, the support structure and figuring path were investigated and determined. Finally, processing experiments were conducted, and the material removal function for the flexible processing tool was computed to shape the reflector surface. The final results achieved the required surface figure accuracies for areas ≤ φ1750 mm, ≤φ2400 mm, and the whole surface were improved to 13.5 μm RMS, 23.4 μm RMS, and 45.8 μm RMS, respectively. This validates the processing capability and demonstrates the potential application of the dual-robot fabrication system in producing large-scale components with high accuracy.
Full article
(This article belongs to the Section Advanced Manufacturing)
►▼
Show Figures
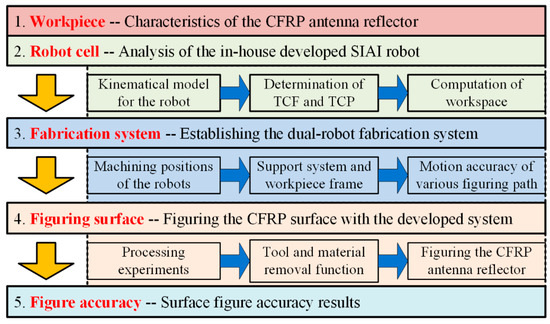
Figure 1
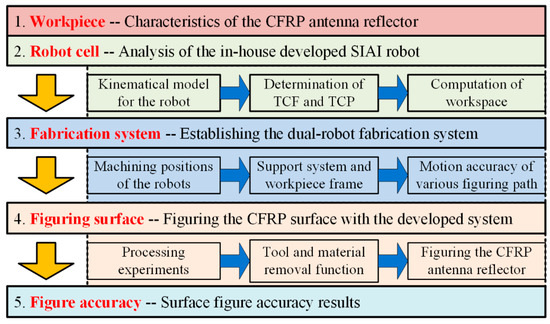
Figure 1
Open AccessReview
A Review of the Industry 4.0 to 5.0 Transition: Exploring the Intersection, Challenges, and Opportunities of Technology and Human–Machine Collaboration
by
Md Tariqul Islam, Kamelia Sepanloo, Seonho Woo, Seung Ho Woo and Young-Jun Son
Machines 2025, 13(4), 267; https://doi.org/10.3390/machines13040267 - 24 Mar 2025
Abstract
The Industrial Revolution (IR) involves a centuries-long process of economic and societal transformation driven by industrial and technological innovation. From agrarian, craft-based societies to modern systems powered by Artificial Intelligence (AI), each IR has brought significant societal advancements yet raised concerns about future
[...] Read more.
The Industrial Revolution (IR) involves a centuries-long process of economic and societal transformation driven by industrial and technological innovation. From agrarian, craft-based societies to modern systems powered by Artificial Intelligence (AI), each IR has brought significant societal advancements yet raised concerns about future implications. As we transition from the Fourth Industrial Revolution (IR4.0) to the emergent Fifth Industrial Revolution (IR5.0), similar questions arise regarding human employment, technological control, and adaptation. During all these shifts, a recurring theme emerges as we fear the unknown and bring a concern that machines may replace humans’ hard and soft skills. Therefore, comprehensive preparation, critical discussion, and future-thinking policies are necessary to successfully navigate any industrial revolution. While IR4.0 emphasized cyber-physical systems, IoT (Internet of Things), and AI-driven automation, IR5.0 aims to integrate these technologies, keeping human, emotion, intelligence, and ethics at the center. This paper critically examines this transition by highlighting the technological foundations, socioeconomic implications, challenges, and opportunities involved. We explore the role of AI, blockchain, edge computing, and immersive technologies in shaping IR5.0, along with workforce reskilling strategies to bridge the potential skills gap. Learning from historic patterns will enable us to navigate this era of change and mitigate any uncertainties in the future.
Full article
(This article belongs to the Special Issue Smart Manufacturing and Beyond: Bridging Innovation in Industry 4.0 and 5.0)
►▼
Show Figures
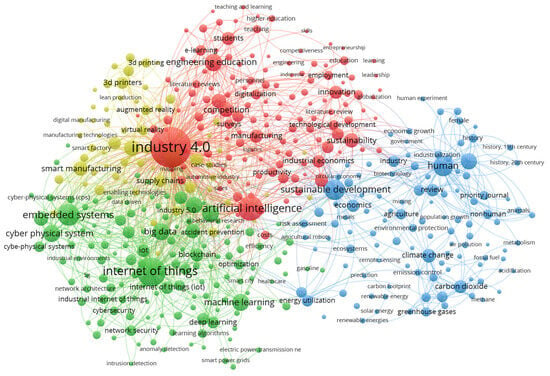
Figure 1
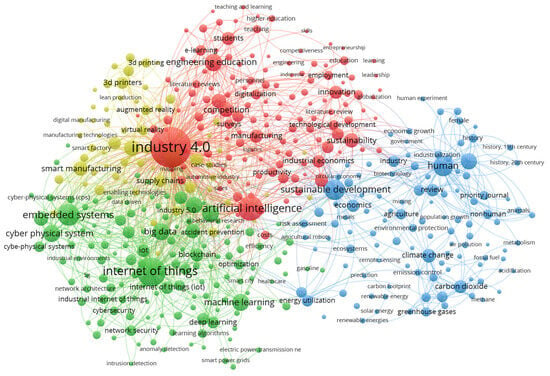
Figure 1
Open AccessArticle
Predictive Modeling of Surface Roughness and Cutting Temperature Using Response Surface Methodology and Artificial Neural Network in Hard Turning of AISI 52100 Steel with Minimal Cutting Fluid Application
by
Sandip Mane, Rajkumar Bhimgonda Patil and Sameer Al-Dahidi
Machines 2025, 13(4), 266; https://doi.org/10.3390/machines13040266 - 24 Mar 2025
Abstract
Hard turning is a precision machining process used in the manufacturing industry for the finishing of hardened alloy steel, which is known for its high hardness and wear resistance. In this work, an experimental investigation was conducted to predict surface roughness and cutting
[...] Read more.
Hard turning is a precision machining process used in the manufacturing industry for the finishing of hardened alloy steel, which is known for its high hardness and wear resistance. In this work, an experimental investigation was conducted to predict surface roughness and cutting temperature during the hard turning of AISI 52100 steel using the minimal cutting fluid application (MCFA). The MCFA is a sustainable high-velocity pulsed jet technique that has emerged as an eco-friendly approach for reducing the environmental impact and improving surface integrity in machining processes. The influence of key machining parameters, such as cutting speed, feed rate, and depth of cut, on the performance indicators was modeled using the response surface methodology (RSM) and the artificial neural network (ANN). The RSM was employed for a structured, statistical analysis, while an ANN provided a data-driven approach for capturing complex non-linear relationships. Various network architectures were established and evaluated with a fixed number of cycles. Results showed that the ANN exhibited superior accuracy in predicting both responses. In comparison to the QR model, the ANN exhibited the lowest average error rate in accurately predicting the response. This was further validated through experimental trials, demonstrating that the ANN consistently outperformed the RSM across different parameter settings. Additionally, the use of the MCFA contributed to sustainable manufacturing by minimizing the use of cutting fluids while maintaining machining quality.
Full article
(This article belongs to the Section Advanced Manufacturing)
►▼
Show Figures
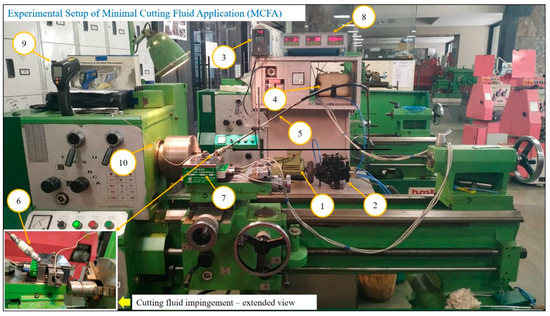
Figure 1
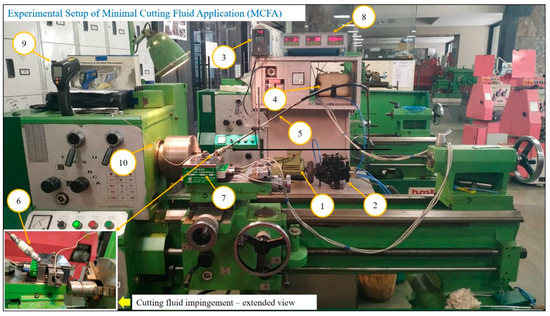
Figure 1
Open AccessArticle
Research on the Conditions and Optimization of 3-UPU Parallel Manipulators That Naturally Realize Three Translational Degrees of Freedom
by
Bo Hu and Peng Bai
Machines 2025, 13(4), 265; https://doi.org/10.3390/machines13040265 - 24 Mar 2025
Abstract
The characteristics of the degrees of freedom (DOFs) of the 3-UPU parallel mechanisms (PMs) are closely related to the orientations of the ending R joints fixed connected with the platforms. The orientations of the ending revolute (R) joints in the Tsai 3-UPU PM
[...] Read more.
The characteristics of the degrees of freedom (DOFs) of the 3-UPU parallel mechanisms (PMs) are closely related to the orientations of the ending R joints fixed connected with the platforms. The orientations of the ending revolute (R) joints in the Tsai 3-UPU PM cannot naturally realize three translational DOFs. First, this paper gives and proves the geometric conditions of the ending R joint fixed to the platforms that can naturally ensure three translational DOFs of the 3-UPU PMs. Second, based on the common motion/force index and good transmission workspace volume of the 3-UPU translational PMs, the performance map of the PMs is drawn, and the corresponding optimization design area of the PMs is obtained. Finally, combined with the obtained optimization design area, in view of the differences in the constraint and stiffness performance of the 3-UPU translational PMs, the multi-objective optimization is carried out using the game theory algorithm, and the orientations of the ending R joints for the 3-UPU translational PMs with good constraint and stiffness performance are obtained.
Full article
(This article belongs to the Section Machine Design and Theory)
►▼
Show Figures
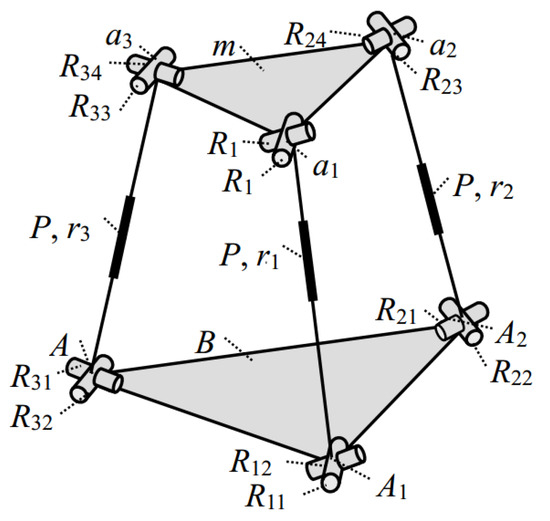
Figure 1
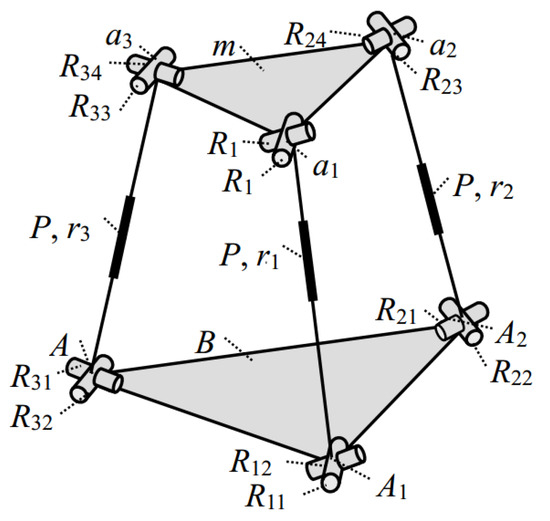
Figure 1
Open AccessArticle
Study on Control Approaches for Servo Systems Exhibiting Uncertain Time Delays
by
Minyu Ma, Shuncai Yao and Weijie Ma
Machines 2025, 13(4), 264; https://doi.org/10.3390/machines13040264 - 24 Mar 2025
Abstract
In response to the uncertainty of delay parameters within the servo control system, an adaptive estimation framework grounded in Bayes–Monte Carlo Markov chain fusion (Bayes-MCMC) is proposed. Subsequently, an uncertain delay estimation model was constructed, and a gain optimization method is put forward.
[...] Read more.
In response to the uncertainty of delay parameters within the servo control system, an adaptive estimation framework grounded in Bayes–Monte Carlo Markov chain fusion (Bayes-MCMC) is proposed. Subsequently, an uncertain delay estimation model was constructed, and a gain optimization method is put forward. An optimal gain state observer tailored to uncertain delays is derived, and a compound control strategy is established to counteract the delay. Experimental findings demonstrate that the observation error of the optimized observer is effectively mitigated. Compared with Smith and the unoptimized gain compensation system, the phase margin, delay margin and gain margin of the system after the gain optimization are increased by 22.8%, 1 order of magnitude, 23.6% and 13.07%, 1 order of magnitude, 1.12%, respectively. Under the condition of delay uncertainty, the system’s output can closely track the given input. The overshoot is effectively reduced, the system’s output response is expedited, the steady-state error is substantially decreased, and the time to reach the steady-state is shortened by around 12.5%. The system’s performance in both the time domain and the frequency domain is remarkably improved, thereby validating the effectiveness and superiority of the proposed method.
Full article
(This article belongs to the Section Automation and Control Systems)
►▼
Show Figures
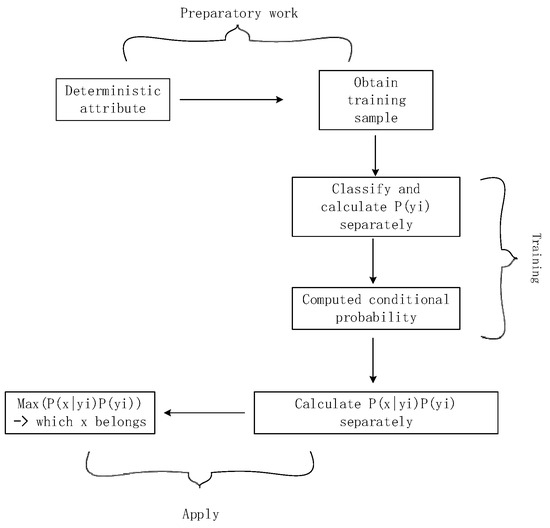
Figure 1
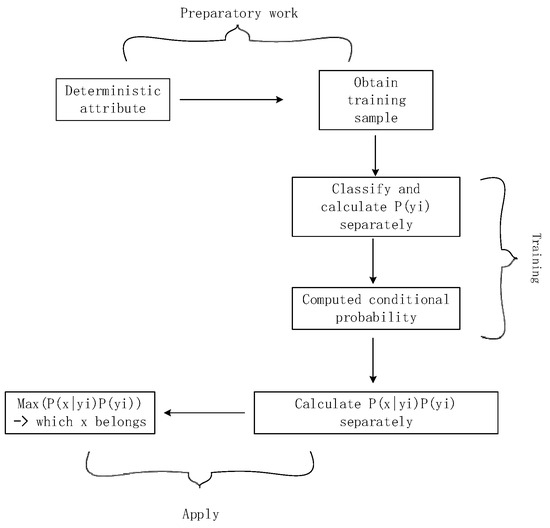
Figure 1
Open AccessArticle
Fault Diagnosis of Reciprocating Compressor Valve Based on Triplet Siamese Neural Network
by
Zixuan Zhang, Wenbo Wang, Wenzheng Chen, Qiang Xiao, Weiwei Xu, Qiang Li, Jie Wang and Zhaozeng Liu
Machines 2025, 13(4), 263; https://doi.org/10.3390/machines13040263 - 23 Mar 2025
Abstract
A fault diagnosis method for reciprocating compressor valves suitable for variable operating conditions is presented in this paper. Firstly, a test bench is independently constructed to simulate fault scenarios under diverse operating conditions and with various faults. The two types of p-V diagrams
[...] Read more.
A fault diagnosis method for reciprocating compressor valves suitable for variable operating conditions is presented in this paper. Firstly, a test bench is independently constructed to simulate fault scenarios under diverse operating conditions and with various faults. The two types of p-V diagrams are gathered, and the improved logarithmic p-V diagram acquisition method is used for logarithmic transformation to obtain the multi-conditional logarithmic p-V diagram dataset and the fault logarithmic p-V diagram dataset. Subsequently, to predict the fault-free logarithmic p-V diagram under different operating conditions, a BP neural network is trained with the multi-condition logarithmic p-V diagram dataset. Next, the fault sequence is derived by subtracting the fault logarithmic p-V diagram from the fault-free logarithmic p-V diagram acquired under the same operating condition. Ultimately, the feature extraction of the fault sequence and the fault classification are accomplished by the employment of a triplet Siamese neural network (SNN). The results indicate that the fault classification accuracy of the method presented in this paper can attain 100%, which confirms that differential processing on the logarithmic p-V diagram is effective for fault feature preprocessing. This study not only improves the accuracy and efficiency of valve fault diagnosis in reciprocating compressors but also provides technical support for maintenance and fault prevention.
Full article
(This article belongs to the Section Automation and Control Systems)
►▼
Show Figures
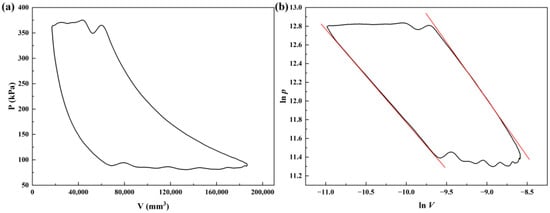
Figure 1
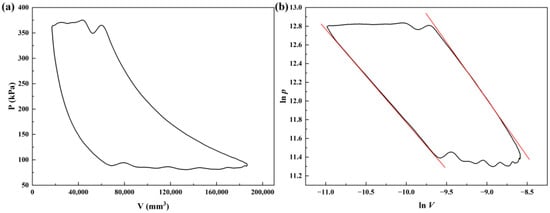
Figure 1
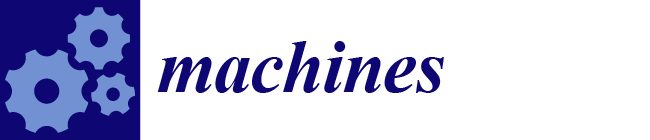
Journal Menu
► ▼ Journal Menu-
- Machines Home
- Aims & Scope
- Editorial Board
- Reviewer Board
- Topical Advisory Panel
- Instructions for Authors
- Special Issues
- Topics
- Sections & Collections
- Article Processing Charge
- Indexing & Archiving
- Editor’s Choice Articles
- Most Cited & Viewed
- Journal Statistics
- Journal History
- Journal Awards
- Society Collaborations
- Conferences
- Editorial Office
Journal Browser
► ▼ Journal BrowserHighly Accessed Articles
Latest Books
E-Mail Alert
News
Topics
Topic in
Applied Sciences, Designs, Energies, Machines, Vehicles
Advanced Electrical Machines and Drives Technologies, 2nd Volume
Topic Editors: Loránd Szabó, Marcin WardachDeadline: 31 May 2025
Topic in
Applied Sciences, Electronics, Future Internet, Machines, Systems, Technologies, Biomimetics
Theoretical and Applied Problems in Human-Computer Intelligent Systems
Topic Editors: Jiahui Yu, Charlie Yang, Zhenyu Wen, Dalin Zhou, Dongxu Gao, Changting LinDeadline: 30 June 2025
Topic in
Applied Sciences, Electronics, IoT, Materials, Robotics, Sensors, Machines
Smart Production in Terms of Industry 4.0 and 5.0
Topic Editors: Iwona Paprocka, Cezary Grabowik, Jozef HusarDeadline: 31 August 2025
Topic in
Electronics, Fluids, Machines, Micromachines, Applied Sciences
Micro-Mechatronic Engineering, 2nd Edition
Topic Editors: Teng Zhou, Antonio F. MiguelDeadline: 31 October 2025

Conferences
Special Issues
Special Issue in
Machines
Sensors and Signal Processing in Manufacturing Processes
Guest Editors: Alain Gil Del Val, Mariluz Penalva, Fernando VeigaDeadline: 30 March 2025
Special Issue in
Machines
Advanced Protection and Control Strategies for Power Conversion in Electromechanical Energy Storage Systems
Guest Editors: Jian Qiao, Luliang Zhang, Xin Yin, Moduo Yu, Yikai Wang, Yayu YangDeadline: 31 March 2025
Special Issue in
Machines
Advanced Power Electronic Technologies in Electric Drive Systems
Guest Editor: Kotb TawfiqDeadline: 31 March 2025
Special Issue in
Machines
Recent Advances in Medical Robotics
Guest Editors: Clemente Lauretti, Alessia Noccaro, Francesca CordellaDeadline: 31 March 2025
Topical Collections
Topical Collection in
Machines
Machines, Mechanisms and Robots: Theory and Applications
Collection Editor: Raffaele Di Gregorio